For Cast In Place Connection
With the traditional connection method, the rebars are placed and lapped together with the adjacent bars during the formwork. The lap length is specified by the building code and generally the bigger the bar diameter, the longer the lap length. Since the lapped splices double the number of rebars at the lapped bar area, taking additional space in the concrete members, rebar congestion sometimes occurs to and interferes with the concrete pour by restricting the flow of concrete aggregates meant to fill the form. Lap splices depend on concrete for strength, and the lower the concrete strength, the longer the lap length required. More materials, more cost.
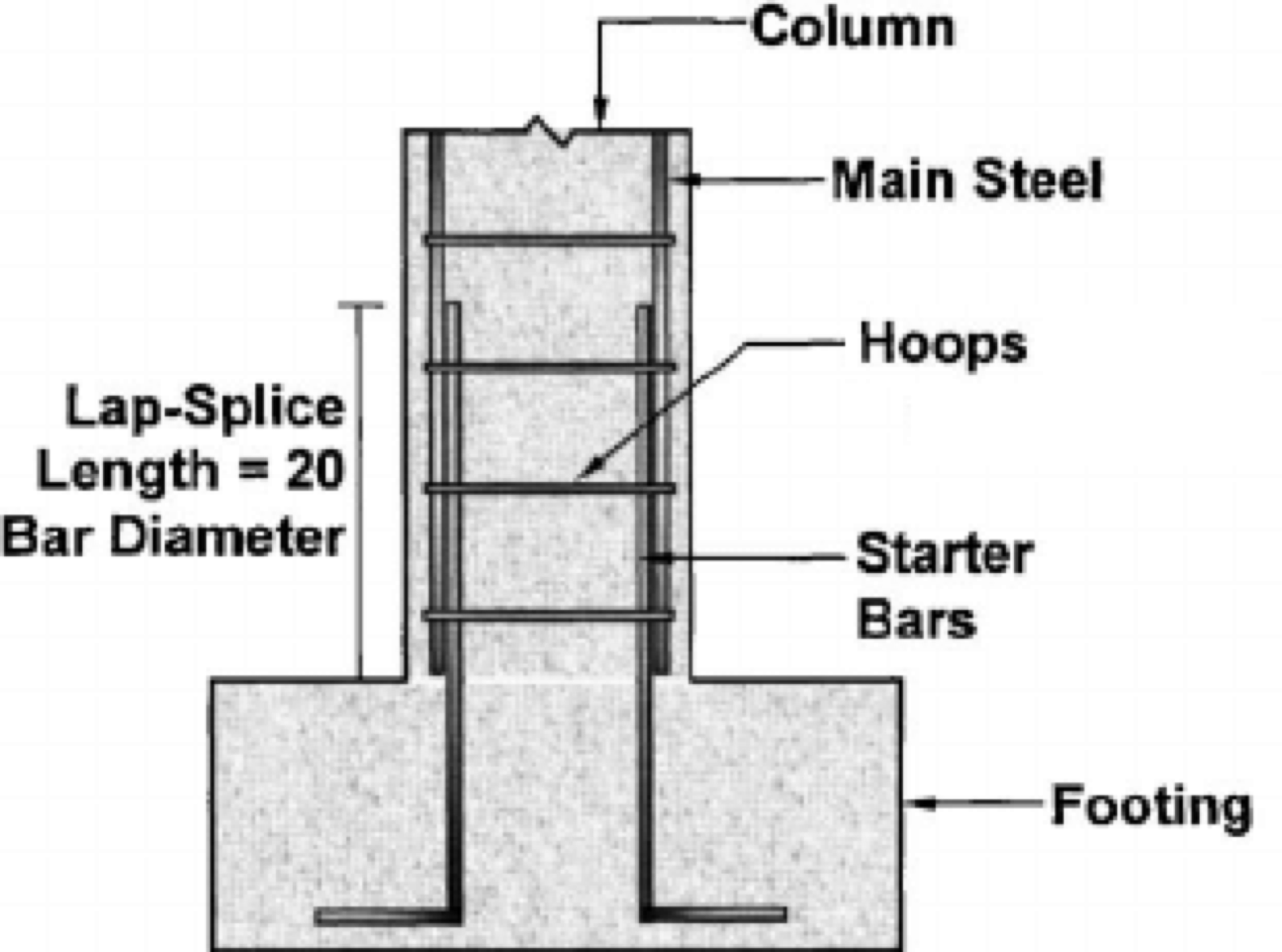
Structural engineers, architects and specifiers have discovered that mechanical splices have many advantages over the lap splices. Mechanical rebar splices for cast-in-place construction generally consist of steel couplers with many types of connecting systems such as threading, squeezing, swaging, etc. and some treatment or preparation required on the rebars to be spliced. NMB Connection is made by butt-splicing the rebars with no lapping and the coupler is relatively small, thus reducing rebar congestion and improving concrete consolidation. The splice strength is obtained regardless of concrete quality.
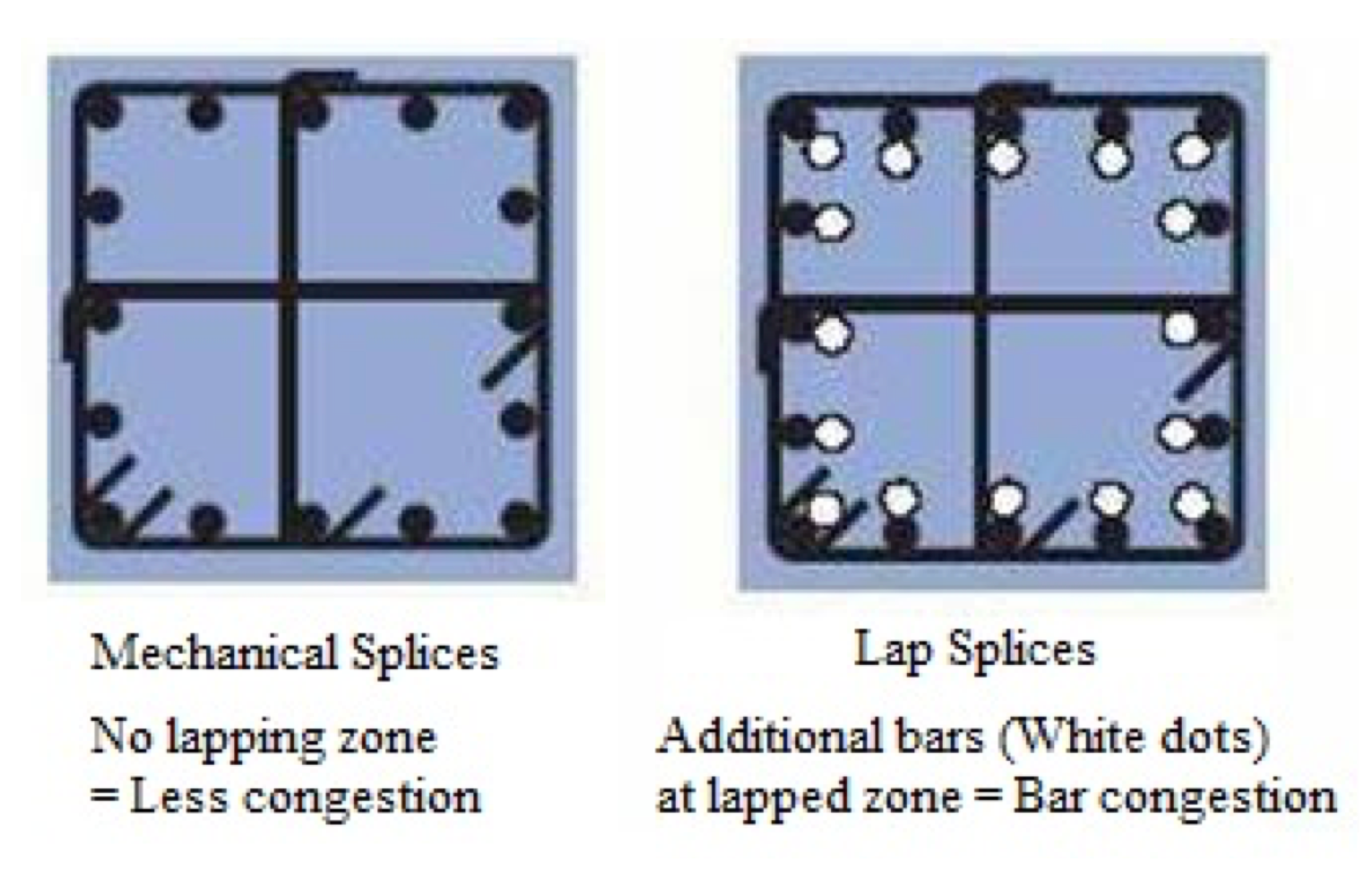
Having all the advantages of mechanical couplers over the lap splices, the NMB Slim-Sleeve was developed for the cast-in-place application. Though relatively new to the construction field, the Slim-Sleeve offers more to the job site.
(See more details at PRODUCTS)
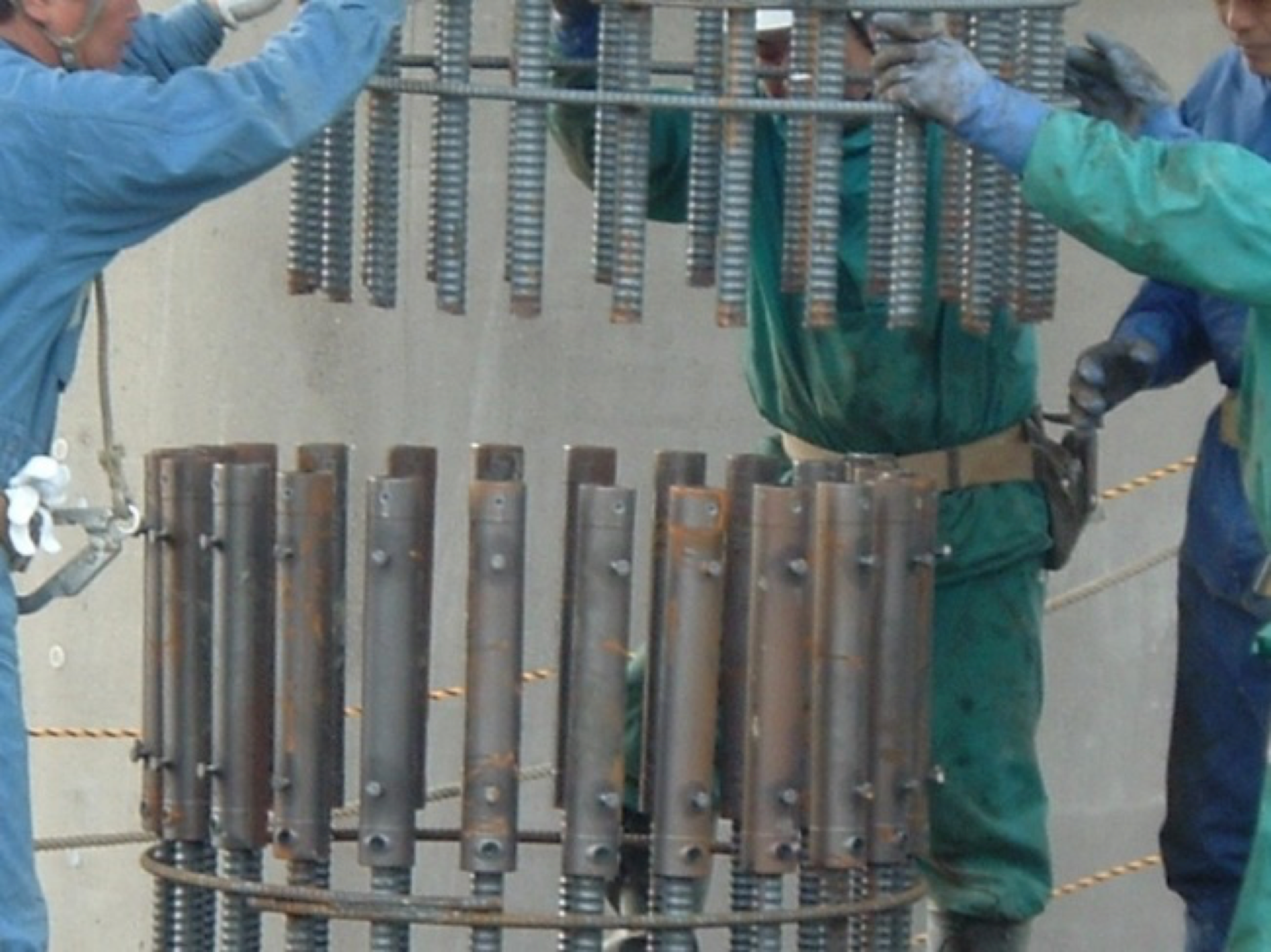